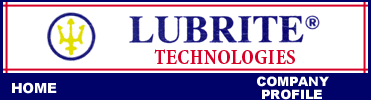 |
|
Design
Engineering
A bearing
is only as good as the engineering and manufacturing skills that go into
it. Capability is evidenced by the long and successful experience of our
engineering staff. The group has at its disposal a comprehensive data-bank
on bearing design and performance. This knowledge is the result of experience
in a wide variety of applications, and is now supplemented by our computer-assisted
design and engineering program. In addition, engineers always stand
ready to provide you with the full benefit of this experience -- from preliminary
design assistance through field engineering. More than 80 years of research,
engineering and manufacturing know-how stand behind every Lubrite® bearing.
Back to top
|
Testing
Laboratory
Lubrite® Technologies maintains a sophisticated
in-house testing laboratory for research and development as well as production
testing. If required, new designs can be tested under simulated field
operating conditions to ensure successful performance. Precise parameters
such as load, speed, and environmental conditions can be duplicated.
Back
to top
Bearing
Materials
A Lubrite® bearing system consists of
two basic components -- the bearing substrate and lubricant. This makes
detailed knowledge on the application of bearing materials extremely important.
The substrate
materials selected for a bearing system can vary considerably based on
the application. Bronze is commonly used, but in unusual environments
other materials ranging from stainless steel and nodular-iron to tool-steel
can be employed. Metallurgical experience assures you of proper selection
and maximum bearing life.
Back
to top
|
Lubricants
Lubricants used in Lubrite® Technologies'
products are compounds or composites dry, solid, permanent, and completely
self-lubricating. They do not require any form of supplementary lubrication.
Decades of research and development have been put into developing lubricants
and they are constantly tested both in our laboratories and in the field
to ensure performance, and to develop further improvements.
A number of
lubricants have been developed to meet the specific needs of a wide variety
of applications. One of these lubricants will provide the operating characteristics
needed for your application.
Back
to top
|
Bearing
Assemblies
Lubrite® Technologies has the in-plant
capability to manufacture extremely large self-lubricating bearings and
accompanying assemblies -- such as the 30,000 lb. bearings used in the
Thames Flood Defense Project in London, England. Lubrite® Technologies
generally supplies all the peripheral parts needed to complete a bearing
assembly, including support systems, structural components, mating pins,
housings, and any other special requirements. The combination of our metallurgical
experiences with an in-house foundry and state-of-the-art welding capability
facilitates manufacturing even the largest assembly parts. Assemblies
as large as 35 tons have been built in our plant. It is recommended that
complete bearing assemblies (including pins, shafts, and all related steel
components) be designed and manufactured by Lubrite® Technologies.
This approach assures perfect mating fits of system components, a fast,
efficient installation, and superior bearing performance.
Back
to top
|
World's largest spherical, self-aligning bearing. This bearing has been
in continuous operation in a harsh environment since 1976, protecting
London from tidal flooding.
|
Machining
Lubrite® Technologies' modern machine
shop with CAD/CAM and CNC capabilities performs all of the machining operations
required in manufacturing Lubrite® products, assuring consistent quality
and on-time deliveries.
Back
to top
|
Welding
Superior welding skills are required to produce
mating surfaces of unusual metals. One example is the use of Submerged
Arc welding techniques by Lubrite® welders to overlay surfaces with
materials such as Inconel 625, Monel, and stainless steel. Lubrite®
welders are qualified to meet the requirements of the AWS structural welding
code and AASHTO.
Back
to top
|
|
Quality
Assurance and Control
The first and most important step in quality
control is quality assurance. Once product specifications are established,
Quality Assurance develops step-by-step manufacturing guidelines to ensure
the finished product will meet your requirements. Each stage in the production
process is then monitored by Quality Control personnel to be certain of
adherence to the guidelines. A reporting system that documents every interval
of the manufacturing process and provides complete traceability is an
important part of the program. Non-destructive testing is done by
personnel qualified to ASNT, SNT - TC - 1A. All destructive testing meets
specifications of ASTM. Every inspection is documented for your reference.
Back
to top
|
Lubrite's
Service
Lubrite® Technologies' philosophy is
one of involvement and committment. Our personnel are always available
to work closely with your own staff. Your customer service contact at
Lubrite® Technologies will help you establish the original design
concept, and then follow through to delivery of the bearing to your site.
Arranging field inspections, handling expediting requests, providing test
and certification documentation, and supplying any other information you
may need are all part of your customer service representative's role in
assuring you of superior service. If you have a special requirement, such
as field engineering assistance after installation, this can also be easily
arranged.
Before, during,
and after startup of your project, you always have the assurance of knowing
Lubrite® Technologies' complete capability is as close as the nearest
telephone.
Back
to top
|
To
Satisfy All Your Self-Lubricated Bearing Needs, Please Contact
Chester Dabkowski at (781) 871-1420 or [email protected]
(e-mail).
|